In December, five members of Local 393 at the Suffolk County Water Authority (SCWA) participated in the first of five planned sessions of “Fall Protection Competent Person” training. SCWA partnered with safety equipment manufacturer 3M to deliver this specialized 16-hour course. A second group completed training in February, and three additional sessions are scheduled for 2025.
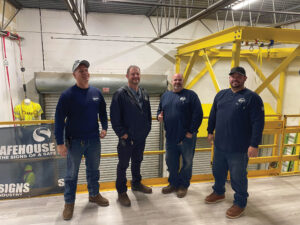
The training followed SCWA’s 2024 safety equipment investment, which included $47,000 for essential protective gear (22 harnesses, self-retracting lifelines, connectors, anchor points, and hard hats), $27,000 for an aerial lift, and $12,000 for fleet mechanic equipment. The authority also plans to acquire lightweight ladders. Each employee’s training represents an $800 investment.
SCWA’s new fall protection training program comes after nearly a decade of advocacy by Local 393 for improved safety measures. Progress had been delayed by management until a proactive safety director was appointed, and the program moved forward.
The program, which was tailored to SCWA’s specific needs, was developed after 3M conducted site visits six months earlier to assess workplace hazards. The curriculum blended theoretical and practical instruction, with 60% of instruction time dedicated to safety regulations and standards. Participants studied OSHA regulations 1910 and 1926, which mandate fall protection for work at heights of 4 feet or more. Topics included tie-off areas, guardrail systems, ladder safety, and proper use of personal protective equipment (PPE).
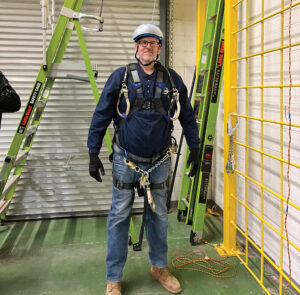
The remaining 40% focused on hands-on applications. Participants practiced wearing and inspecting harnesses, evaluating anchor points, and scaling a 35–40-foot wall using lanyard hooks and locks for hands-free operation. The program also emphasized tool safety to prevent injuries from falling objects, providing valuable insights even for experienced safety committee members.
Ronnie Brooks, who works in SCWA’s electrical department and serves on the UWUA’s National Safety Committee, emphasized the training’s importance: “In the electrical department, we often work on rooftops 10–15 feet high, removing roof hatches to access equipment and lowering motors into gazebos and vaults. Without proper safety protocols, vault falls can cause serious injuries.”
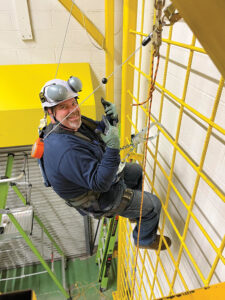
Jeremy Terhune, a shop steward for SCWA’s mechanics, played a pivotal role in highlighting the urgent need for fall protection training for mechanics. He explained that both mechanics and electricians frequently work on top of various types of treatment filters, which range in height from 15 to 50 feet: “These filters often have curved and slippery surfaces that pose significant fall hazards.”
The authority manages 250 sites and 600 wells, many housed in vaults and gazebos. “Summer brings increased motor failures requiring repair or replacement,” Brooks said. “Our electricians and mechanics maintain these motors, working with 480-volt systems, primary and secondary wiring, control wiring, valves, actuators, and generators.”
Brooks emphasized the value of knowledge and competence in advocacy, crediting Local 393’s safety chair, Donnie Blumberg, for his persistence and dedication.
UWUA National Safety Director Scotty MacNeill highlighted the broader implications of this success: “This achievement shows the power of locals to negotiate stronger workplace safety measures, whether through enhanced training, improved PPE, or both. It underscores the importance of verifying safety conditions rather than taking management’s word. Your life depends on understanding proper protocols. Follow Local 393’s example: educate yourselves, stay persistent, and utilize the National Safety Committee’s expertise to create safer workplaces.”