UWUA leadership recently attended an event at the Palisades Nuclear Generating Station in Covert, MI, hosted by the Department of Energy (DOE) and Holtec. The event celebrated the Biden administration’s conditional commitment of a $1.52 billion loan guarantee to restart the facility, marking the first time a nuclear plant would be brought back online after being decommissioned.
This loan commitment, along with two long-term Power Purchase Agreements (PPAs) for the plant’s full power output with rural electric cooperatives in Michigan, Illinois, and Indiana, represents a significant step toward restarting the facility.
As part of the event, UWUA Executive Vice President Patrick Dillon participated in a panel discussion moderated by DOE’s Loan Programs Office Director, Jigar Shah, and the U.S. Department of Agriculture’s Administrator of Rural Utilities Service, Andy Berke.
“These aren’t just jobs at Palisades; these are careers,” Dillon remarked during the panel. “That’s the value of hiring on, not just at Palisades but in the utility industry. When you hire into the utility industry, you’re hiring into a career.”
The event highlighted the various ways Palisades’ reopening could impact the power grid, the economy of Southwest Michigan, and, notably, the jobs and futures of UWUA members.
Aubery Watson, president of Local 150, which represents workers in operations, maintenance, chemistry, radiation protection, and warehousing at Palisades, noted that UWUA’s presence at the plant dwindled to 33 members at one point. Since restart efforts began, Local 150 has about 140 members working at the plant, with the local’s total membership now at 380.
Lonzey Taylor, a long-time Local 150 member, retired in 2022 after 46 years at Palisades. However, Holtec persuaded him to postpone his retirement to help train the next generation of nuclear power operators.
Pat Dillon spoke to Taylor about his experience at the plant and what this milestone means for the future. Their conversation appears below, edited for clarity and brevity.
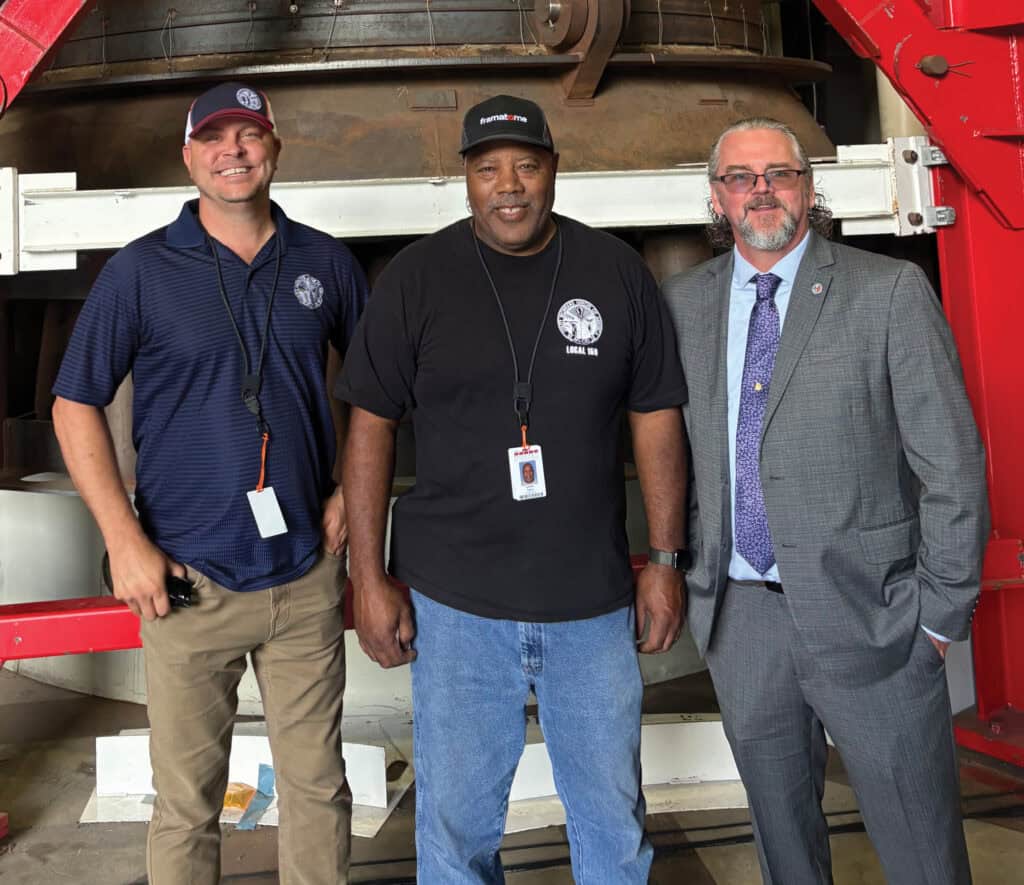
PD: What are you training members on right now?
LT: I’m training mechanical, everybody from top to bottom including material handling, rigging. We’re going on forklifts, articulated booms, cranes. Then we’re getting ready to do the skillsets, pumps, valves, then the specialty skills. We’re trying to get the crew up to snuff before they start. That’s the biggest thing; this place can have all the hardware ready but not all the skilled people.
PD: Do you have any really green people, brand new to the industry?
LT: Yes. The challenge we have is breaking habits. You don’t let common sense come into the plant because things you would do out in the world, you can’t do in here. You may sit for five hours waiting on a decision to put a half inch bolt in there. If you’re out in the world it’s production, production, production. Here, it’s all about safety. It’s all about following the procedures. So it’s hard to break that habit.
So what I would say to nuclear people, come in with the attitude of learning. Learn the trade. You can travel all over the world. This place has afforded me the ability to travel all over the place.
PD: You lived here at the plant. You’re a fixture. And it was your plant; you took it personally.
LT: Yes, it was pride. Have pride in what you do. If you worked on that pump, you’re concerned if that pump fails because it’s a reflection on you.
PD: What was your last classification when you retired?
LT: Lead repairman. I was basically a working foreman. For years, I was the only lead in the shop. I ran the shop. I had green supervisors, a green superintendent, and they relied on me to run the shop.
PD: In the nuclear industry, management changes rapidly and you’re always working for someone new.
LT: It was unprecedented. They went to the union to give me a bonus for the work I did, and they don’t normally do that. It was good.
PD: How much have things changed or not over 46 years since you started work at Palisades?
LT: It’s changed a lot since I started — back when I was 17 years old. At that time, we didn’t have all the procedures, policies, practices; checks and balances; or the piping and redundant systems we have today.
Security has also changed. We didn’t have armed guards; in fact, there was just one person at the checkout. Other than that, you could drive right into the plant. The fencing and lake access have changed, too. We used to be able to go out to smelt dip, salmon fish, and things like that — it was common until 9/11. In fact, it was like a marina here, with boats docking nearby because of the warm water that comes out of the plant.
In the end, I believe the world will be coming to you, asking, “How did you do it? How did the company work with the unions? What kind of give and take was there?” I know we transitioned from a decommissioning phase, where everyone handled multiple roles, to a time when we started drawing clearer boundaries. But as long as everyone works together, it’ll work. The company needs the union, and the union needs the company. There’s a mutual need on both sides. If it stays that way, I think things will turn out great.