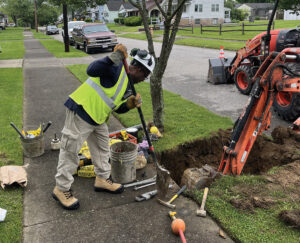
Natural gas, composed primarily of methane, is highly flammable and can pose significant risks if mishandled. It takes special training and skills to safely transport and deliver to customers. Our members’ diligence and expertise are paramount in safeguarding communities and ensuring that natural gas continues to be a reliable and safe energy source for homes and businesses alike.
Natural gas undergoes a complex journey before it reaches our stoves and heaters. The process begins with extraction from underground reservoirs through drilling. It travels through pipelines to processing plants where impurities like water, sulfur, and carbon dioxide are removed, ensuring safety and purity. From there, it enters high-pressure transmission pipelines, spanning vast distances. These pipelines are essential for delivering gas to regional distribution centers. At these centers, the gas pressure is reduced, making it suitable for local distribution through an extensive network of smaller pipelines buried underground. The members profiled here work in this final stage of the distribution journey, ensuring that natural gas arrives safely at homes and businesses.
Jose Croal
Local G-555
Senior Gas Technician, Construction and Maintenance
Enbridge Gas Ohio
I’ve been working in natural gas and have been a member of Local G-555 for 38 years. I started out as a meter reader and did that for three years before moving over to construction and maintenance, where I’ve worked ever since. It’s a long learning curve to get to the top classification, and I worked seven years to reach a position as a senior gas technician. Ohio law requires gas technicians to re-qualify every three years, so my coworkers and I are in near constant schooling — both in the classroom and out in the field. We’re tested to ensure we’re always current on our skills and knowledge.
Most of us work as part of a two- or three-member crew, with two more senior workers and one trainee, and you don’t always work with the same people. It’s hard, physical work. I have high seniority so for the past three years, I’ve been driving a dump truck that delivers supplies and picks up materials from job sites where we’re doing repairs and maintenance on gas lines.
We work on both residential and commercial service lines. Every day is different depending on what kind of emergency is happening. We may get a call that a residence doesn’t have gas or someone has hit a meter and caused a leak. Other times, construction crews digging sewer lines may accidentally damage one of our gas lines. Whenever there’s a leak, we need to shut down the flow, fix any damaged pipes and valves and get them back to working order. Some days, we’re dealing with replacing a corroded pipe or a main line leak. We may have to use a backhoe to dig up the line to gain access for the repair.
Tara Belvedore
Local 132
Lead Construction Technician
SoCal Gas
I work in Los Angeles. I started working in distribution about five years ago as a construction technician on a work crew. After two years, I took and passed a 6-week welding course and applied for a lead position.
For the past three years, I’ve been running my own 2 to 4-person crew each day. I don’t know what will be on my schedule until I arrive at the yard in the morning to pick up my truck and crew. Every day is different and that’s part of what I like most about the job.
We do everything from repairing leaks on gas meters to installing whole new main lines in downtown Los Angeles. On a recent day, we were installing a steel service line to a new building but weren’t detecting any odor — which is a red flag. We pulled together a joint task force that included my crew and representatives from SoCal’s lab and engineering departments. We re-seasoned the pipe and got it back in working order.
Days can change from hour-to-hour, too. We may start the day thinking a job is going to take all day but end up finishing in two hours. We then get a call that a line has been hit and are immediately on our way to do a repair that may take all night.
A little over half of my work relates to responding to emergencies; much of the rest is connected to new construction that is always going on in L.A. In a city with constant building and construction, gas lines are often damaged and require repair.
Even though I work a regular 6:30 AM to 3 PM day shift, sometimes we plan special projects at night since we’re working downtown and want to avoid creating traffic gridlock. The city has regulations on the time of day that certain types of jobs can be done so we need to work around those. It’s safer for us, too, to avoid shutting down lanes during times when a lot of people are on the road.
When I started with SoCal Gas 10 years ago, I worked as a meter reader for about year before switching to customer service, where I went into customers’ homes and businesses to fix appliances like furnaces, water heaters and dryers. After three years, I was ready for a change. I passed a physical test to qualify for distribution and found what I was looking for.
To keep my job, I’m required to recertify in welding every year and maintain certifications in other areas like plastics and hot season on metal pipes that are on three-year cycles.
Bruce Edwards
Local 1-2
Senior Designer, Gas Engineering
Consolidated Edison
I spend my days in an office responding to customer requests for natural gas service additions or changes in Westchester County, New York. ConEd has 10 million electric, steam and gas customers spread over four counties — Westchester, Bronx, Manhattan and Queens — and each county is served by two or three gas designers. The company has a similar engineering set up for its electric and steam divisions.
Most of my work involves addressing customer requests for new services. This can be a simple task like a homeowner wanting to replace an electric oven with a gas range or something a little more complicated like an apartment building owner wanting to convert from oil to gas heat. Customers first contact ConEd’s Energy Services Department, which forwards the request to engineering for an assessment.
I’m fortunate to have a bird’s eye view of the whole system. Our system has low-, medium- and high-pressure service lines. The higher the pressure, the greater the capacity for adding new services without involving new construction. I also know where the infrastructure is older and where we’ve upgraded.
Whatever the request, I’ll check our system from an engineering aspect to see if there’s adequate pressure coming in to support the new service. If so, the customer is all set and can move forward. If not, I’ll ask the Energy Services Department to send me basic information on the customer’s current set up, such as where their current service line is located and how far it is from the main. Then I’ll use a computer design system to draw up a plan for a field crew to implement. It will include specifications such as whether a regulator is required, where the meter should go, and where to place the curb valve. When I finish a design, I send it to my supervisor for review, and from there it will go to the Energy Services Group to manage the field process to get the work done.
On a typical day, I may address between five and 10 of these types of small service requests. Sometimes, we get requests for revisions because field conditions may have changed, or the customer decides to add two new gas appliances instead of the one initially planned.
For bigger projects, like new construction of a large building or a multi-home development, I’ll send the request to a special engineering group for a load study to determine whether the current system can support the addition or if we need to add main capacity to meet anticipated demand. These take longer to complete. A plan for a big residential development that is being built in phases and requires all new mains and services may take years to map out and finalize.
I’ve been with ConEd for 16 years. I have an associate degree in electrical technology and spent three years in steam engineering before switching to gas. I’ve been a senior designer for the past 10 years and am proud to serve as cochair of the Local 1-2 Gas Union Safety Committee.