Companies have been adopting “Lean” process, a methodology focused on creating value with fewer resources and less waste, since it was first introduced in the 1930s. In theory, Lean calls for ongoing experimentation by workers and managers to find ways to improve quality and flow, reduce time and effort, and lower costs. It involves collaboration, continuous learning and adaptation.
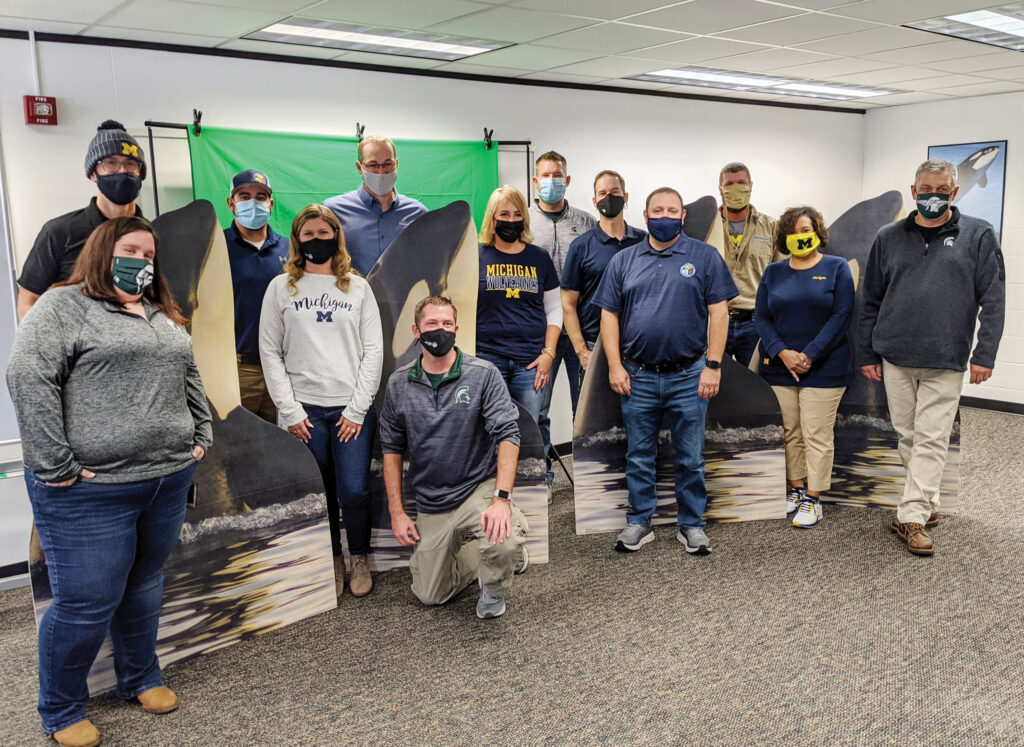
In practice, many companies use Lean to rationalize cost-cutting. That’s what the Michigan State Utilities Workers Council (MSUWC) suspected in 2013 when Consumers Energy hired a new CEO and several former auto industry executives intent on applying Lean. UWUA Executive Vice President Pat Dillon led the MSUWC at that time and recalled, “It was pretty clear to us that they looked at Lean as a way to streamline processes that would result in job elimination.”
According to Vic Phillips, former president of Local 354 who stepped down to become the MSWUC’s first full-time field operations process representative in 2017, “We saw the writing on the wall. The company was going to implement Lean no matter what, and Pat Dillon convinced the MSUWC board to be proactive, just like we had done with safety back in 2005, so we could take control of the process and protect our jobs.”
Local 129 President and Part-Time Process Representative Ben Hatler recalls a day five years ago when the union was at safety meeting with the company and Vic Phillips said, “We’ve done such a good job with safety, when are you going let us help fix the business’s other problems?”
Today, the MSUWC has eight full-time and one part-time process representative, a joint labor-management field operations support (FOS) team and 23 more localized “fix-it-now” (FIN) teams tasked with improving workflow and reducing waste. They work together to problem solve on a range of issues, always engaging the people closest to the work. Not a single UWUA job has been lost; in fact, several new positions have been added. Hatler emphasized that a lot of people think of Lean as doing more with less people, and said, “That’s so far from what we’re about. Our focus is on small, incremental improvements that can be achieved with tweaks to the process.”
“To be effective, we redefined what Lean means,” said Phillips. “We train our own members on how to problem solve and how to look to reduce waste in their job in a way that improves the way we work.”
He shared an example of how the storeroom staff used to conduct inventory by hand entering items. “The products they were logging had bar codes, so we said, why not get a bar code scanner, saving hours of data entry and allowing the staff to move on to other tasks?” This simple fix had the added benefit of eliminating the human error associated with hand entry.
Another example involved redirecting how the company looked at the issue of getting work teams into the field each morning. Phillips explained, “Management was so focused on departure time and didn’t realize that our members were having to re-fuel trucks, conduct maintenance and deal with mechanical issues before they could start their real work.” The process team sought worker input, resulting in the creation of 11 union mechanic positions to fuel and maintain trucks and conduct preemptive maintenance on equipment. Field teams now leave the lot on time with trucks that are ready for the day’s tasks.
In just five years, Consumers has come to see the union as an equal partner on process, mirroring the success of their safety collaboration. Hatler added that process and safety go hand in hand: “A lot of safety concerns come out of bad processes.” The process work has been so successful that other companies now come to Consumers to benchmark.
Phillips and Hatler both emphasize that a big part of the job is changing the mindset of both management and front-line workers away from “that’s the way we’ve always done it.” “If you can challenge people to think differently, these little changes ultimately add up to greater efficiencies,” said Hatler. Phillips added, “We’re not necessarily focusing on money saving, but frequently that’s the end result. When the company sees the savings, it gives the union more say.”
Looking back to when Consumers first announced Lean’s adoption, Dillon reflected, “Quite often as a union, our reaction is to fight them. But if you can insert yourself into the process and become indispensable, you can direct the agenda.”